More than a Thealing! Marketing goes Undercover
The Marketing team are always on hand to visit our Aggregates & Asphalt (A&A) plants to capture a behind-the-scenes look into the lifecycle of our products. Take a look with us as we uncover the journey of our aggregates before they reach their final surfacing destinations, taking a closer look at exactly how our products are manufactured, as well as how our plants are serving local businesses.
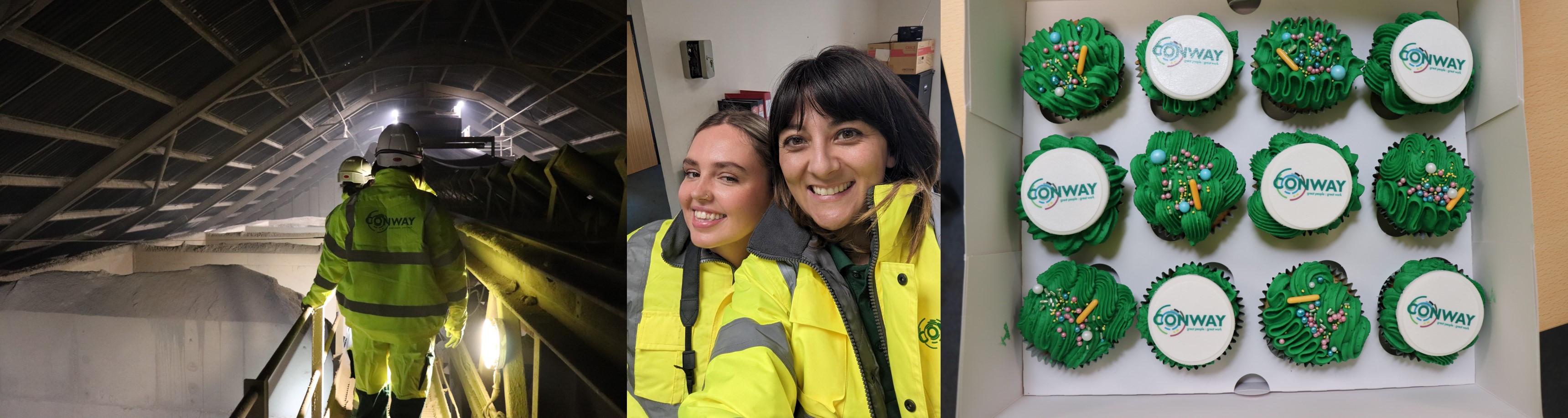
Sharing first-hand knowledge on how each of our plants operate and understanding where they fit within the wider business and self-delivery model is key to our communications. Today, you’ll learn what makes our plants unique and meet the people behind the craftmanship – plus, we are always looking for opportunities to celebrate the work of our Great People!
First up was a trip to our Theale plant, which has two stand-out features: its unique undercover structure, together with a railway depot bringing in virgin aggregate materials. Raw materials including limestone, granite and gritstone are delivered directly into Theale.
Remarkably, aggregates are transported straight from the railway depot onto a conveyor belt, into one of 20 large concrete storage bins, ready to plunge through a hatchway and into the asphalt plant, ready to be mixed and supplied to our customers. It’s an efficient and sophisticated process that the team are very proud of. More importantly, transporting aggregates by rail removes the need for truck journeys from the UK’s roads, helping us to minimize our carbon emissions to net zero.
The height and length of the impressive conveyor belt is just one of the notable features unique to Theale. During our visit, we were also lucky to get a birds-eye-view of the aggregates dropping from the sizeable concrete bins, onto a conveyor belt to feed the asphalt plant.
Originally built in 1981, the Theale plant now operates as a warm mix asphalt plant, and has five bitumen tanks, including one Polymer Modified Bitumen (PMB) tank and an onsite laboratory, underpinning our unique self-delivery model providing our clients and partners with access to low carbon and high-quality recycled materials.
Plant Manager Simon Hawthorn was on hand to give us a warm welcome and an insightful introduction to plant life. We learned about his long stint in the industry and witnessed what a typical day looks like with his team of supervisors, fitters, operatives, drivers, mixers, and a lab technician.
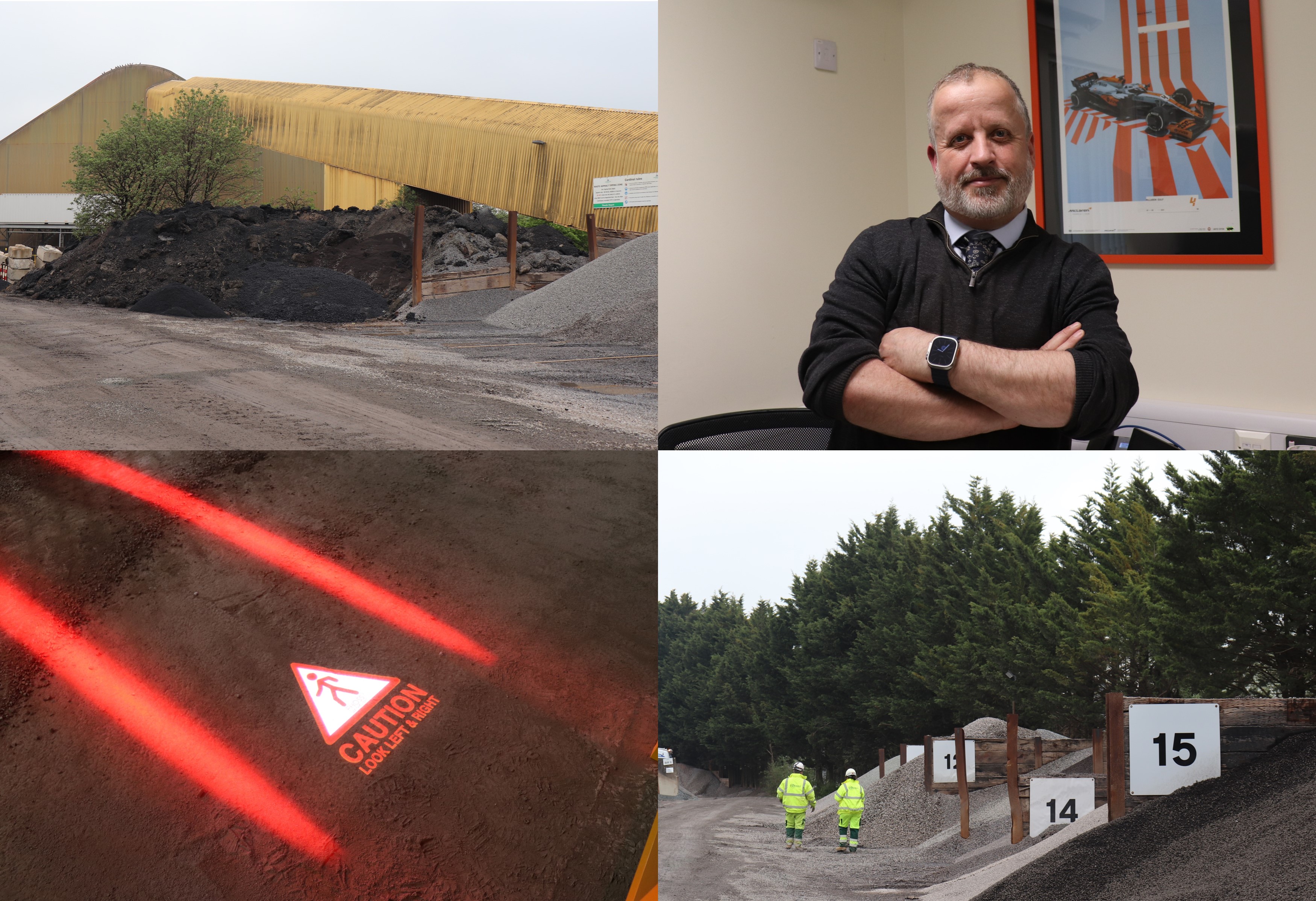
Simon, who is also a Reading FC and Formula One supporter, has worked in the industry since the age of 21 and admits to being competitive, both on the tennis court and on the plant, having owned up to gazumping his twin brother to his first post having both applied for the same job.
We asked Simon what he is most proud of, and his answer was ‘I’m proud of my knowledgeable team and what they have achieved’. Last year they reached a manufacturing record and Simon thanked them for their success in maintaining the plant at all times.
He likened looking after the plant to looking after a car and said how he’s committed to maintaining their excellent health and safety track record. Recent updates, like installing a remote-operated dust suppression system and a laser safety pedestrian walkway, have no doubt helped contribute to their positive outcomes.
You can capture Simon and his remarkable plant in action in this short Instagram reel
here.
Stay connected on our socials to learn more about plant life in the coming months.